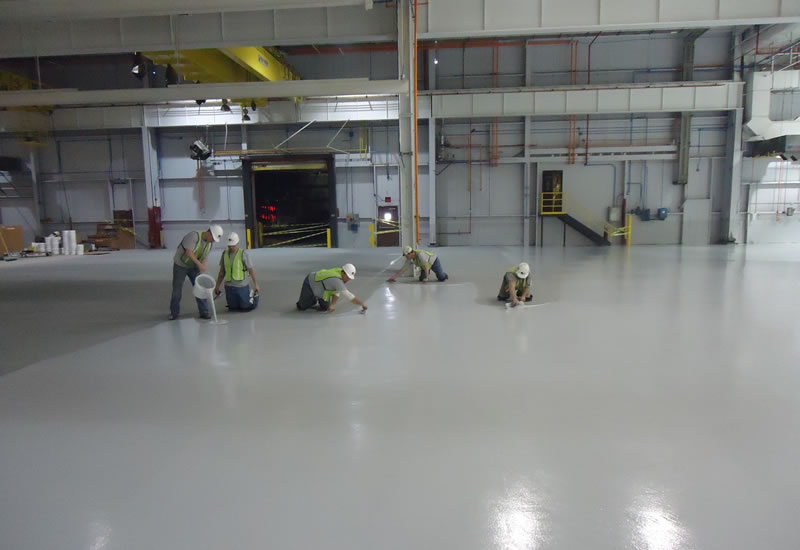
A protective coating is a layer of material applied to the surface of another material with the intent of inhibiting or preventing corrosion. A protective coating may be metallic or non-metallic. Protective coatings are applied using a variety of methods, and can be used for many other purposes besides corrosion prevention.
The protective coating protects in several different ways:
- The copper commonly used for the tracks will be corroded by exposure to oxygen in the air, and the protective coating (a passivation layer) puts a barrier between the oxygen and the metal)
- If the copper must be accessible, either for soldering (on to pads) or for electrical contact (such as edge connectors off the PCB), then the copper is plated with another metal such as tin or nickel. This additional metal forms a passivation layer that protects the copper from oxidation.
- Where the copper need not be accessible, then an electrically insulating protective coating is applied over the metal. This has the additional advantage of preventing dirt and moisture from reducing the insulation resistance between the tracks.
- The insulating material used in the substrate (e.g., FR-4) will readily absorb moisture from the air, thereby reducing the electrical properties of the substrate. The protective coating puts a barrier between the substrate and the moisture in the air.
- The protective coating also controls the flow of solder during the soldering process. This prevents solder from jumping across tracks and causing short